凹版印刷的常見問題及處理方法
1、出現(xiàn)刮刀線或油墨線。原因有:刮刀磨損或刮刀上粘有臟物;油墨中混入雜質(zhì);油墨細(xì)度不夠;印刷版打磨不好,過于粗糙;油墨粘度太高。處理辦法:
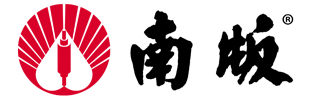
a)如果刮刀線是隨著刮刀的左右擺動(dòng)而有規(guī)律的左右移動(dòng),則可判定是刮墨刀磨損或刮墨刀上粘有臟物,可用竹簽在起刀線的部位將臟物清除;如是刮刀磨損,則應(yīng)立即打磨刮刀或更換新刮刀。
b)在印刷中所有油墨都須過濾。盡量使用新墨。
c)油墨顆粒太粗、細(xì)度不夠,易出現(xiàn)線條,用細(xì)度計(jì)檢測(cè)油墨細(xì)度,如細(xì)度不夠需要換油墨。
d)印刷版打磨不好或版面上有細(xì)小硬塊,可先用細(xì)砂紙?jiān)谟∷婷嫔蟻砘卮蚰?,如仍不能解決,需退鉻重鍍。
e)定時(shí)測(cè)量油墨粘度,保持油墨粘度的穩(wěn)定,有條件的廠家可使用油墨自動(dòng)粘度控制器。
2、印刷水紋。出現(xiàn)水紋的原因主要有:油墨的粘度太低;印刷版雕刻太深;油墨的流動(dòng)性不良。處理方法:
a)適當(dāng)提高油墨粘度。
b)提高印刷速度。
c)調(diào)整刮刀角度成稅角。
d)版雕刻太深無法調(diào)整的需要重新制版。
e)改良油墨的流動(dòng)性。
3、油墨回粘。出現(xiàn)印刷回粘的原因主要有:溶劑過慢干,油墨的干燥性不良;印刷過程中收卷壓力太大,印刷后疊放壓力過大(特別是高溫天氣);冷卻水溫度太高,起不到冷卻效果;烘干箱的溫度過高,風(fēng)力過大使油墨出現(xiàn)假干現(xiàn)象;印刷膜的非印刷面表面張力大(或雙面電暈的情況),使薄膜非印刷面上油墨的親和力大,油墨發(fā)生轉(zhuǎn)移。處理辦法:
a)更換為快干熔劑,使油墨充分干燥。
b)調(diào)整收卷壓力,盡量放小。收卷的卷徑不要太大,堆積重量要小。
c)檢查印刷機(jī)的冷卻水是否打開,水溫是否符合要求。
d)調(diào)整烘箱溫度及風(fēng)力,一般在50~65℃為宜。
e)屯刷前檢測(cè)薄膜的表面張力,印刷面的表面張力要大于非印刷面,雙面電暈的薄膜最好不要使用。
4、印刷色差。出現(xiàn)印刷色差的原因主要有:刮墨刀的位置、角度、壓力發(fā)生變化引起印刷色差;油墨粘度變化引起印刷色差;油墨色濃度的變化引起印刷色差;印刷版印到一定量后已變淺;印刷版堵版引起印刷色差;多色混合配置專色時(shí),如果混合油墨中個(gè)顏料的比重相關(guān)較大,在印刷過程中,如油墨循環(huán)不良易發(fā)生油墨沉淀從而引起印刷色差。處理方法:
a)適當(dāng)調(diào)整刮墨刀的位置、角度、壓力,使印刷色相基本保持一致。
b)定時(shí)測(cè)量油墨粘度,保持油墨粘度的一致,有條件的廠家可以配備油墨粘度自動(dòng)控制器。
c)調(diào)整油墨的色濃度(在油墨中添加原墨或沖淡劑),保持色濃度的一致。
d)印刷版退鉻重鍍處理或印版重制。
e)使用印刷版清洗劑清洗版輥。
f)檢查油墨的循環(huán)系統(tǒng),保持油墨流動(dòng)良好。
5、靜電故障。塑料薄膜在印刷中由于磨擦產(chǎn)生靜電。靜電對(duì)印刷品的質(zhì)量危害較大,嚴(yán)重的還會(huì)引起火災(zāi),在印刷過程中要特別注意。薄膜靜電可引起的印刷故障主要有:在印刷圖文的周圍引起“胡須”狀的油墨絲;實(shí)地部分印刷時(shí)會(huì)出現(xiàn)斑駁狀;油墨轉(zhuǎn)移不上,產(chǎn)生空白部分。薄膜靜電雖不能完全消除,但在印刷過程中可以進(jìn)行適當(dāng)?shù)奶幚?,避免產(chǎn)生靜電故障。主要的處理方法如下:
a)適應(yīng)提高車間內(nèi)空氣溫度。
b)適應(yīng)提高油墨的印刷粘度。
c)印刷溶劑中適當(dāng)增加醇類、酮類溶劑的比例,但不可添加過冬,否則會(huì)影響后工序的復(fù)合強(qiáng)度。
d)設(shè)備安裝靜電消防裝置且要經(jīng)常維護(hù)、檢查。
6、印刷泛色(霧版)。刮刀未能將印版上非圖文部分的油墨完全刮干凈,導(dǎo)致油墨轉(zhuǎn)移到印刷基材上的現(xiàn)象稱之為泛色,又稱霧版。引起印刷泛色的主要原因有:印刷版的精度不足、偏心、鍍鉻不良;刮刀壓力不足、角度不適;油墨的印刷粘度過大;車間的環(huán)境濕度太大,使油墨的流動(dòng)性變差;醇類溶劑添加比例過大,導(dǎo)致油墨溶解性不良。處理方法:
a)提高版輥的制造精度。
b)增大刮刀的壓力,調(diào)節(jié)刮刀角度為60~70度,兩切點(diǎn)距離為50~60CM為宜。
c)適當(dāng)降低油墨的印刷粘度。
d)調(diào)整溶劑配方,減少醇類溶劑比例,適當(dāng)增加酮類溶劑的比例。
干式復(fù)合的常見問題及處理方法
一、復(fù)合膜剝離強(qiáng)度不夠
分以下幾種情況:
膠水固化不完全,剝離開來的時(shí)候在膠水面還有粘性。原因:
1、粘合劑的配比錯(cuò)誤,固化劑的比例不足導(dǎo)致固化不完全。在配制粘合劑時(shí)要按粘合劑生產(chǎn)廠家規(guī)定的配比參數(shù)進(jìn)行配制;
2、溶劑的純度不夠,溶劑中含有水或醇類超標(biāo),水或醇類與膠水中的固化劑發(fā)生反應(yīng),降低的固化劑的比例導(dǎo)致膠水固化不完全。用于干復(fù)的溶劑是乙酯,所以乙酯在進(jìn)廠時(shí)每一批都要抽檢,如發(fā)現(xiàn)醇度不夠時(shí)不可使用;
3、印刷膜中油墨的殘留溶劑高引起膠水固化不夠。油墨(特別是PET油墨)的殘留溶劑有一部分會(huì)與膠水中的固化劑發(fā)生反應(yīng),從而消耗了固化劑導(dǎo)致膠水固化不夠。對(duì)策:①薄膜印刷好后最好不要立即復(fù)合,如果時(shí)間允許的話可先放置1-2天后在進(jìn)行復(fù)合;②印刷膜下機(jī)后檢測(cè)殘留溶劑,如殘留溶劑高,在復(fù)合時(shí)可適當(dāng)增加固化劑的比例;③選用快速固化的膠水。
4、復(fù)合膜熟化溫度低、熟化時(shí)間不夠,了出現(xiàn)交聯(lián)不充分,固化不完全。對(duì)策:提高熟化溫度或選用快速固化的膠水。
二、復(fù)合薄膜的表觀問題
1、小墨點(diǎn)。一般復(fù)膜后馬上出現(xiàn)的可能性較小,除非是渣渾雜質(zhì)等。復(fù)膜后一段時(shí)間的鍍鋁膜有可能出現(xiàn)這種現(xiàn)象,原因是因?yàn)橛湍珜?duì)鋁的腐蝕,當(dāng)油墨呈現(xiàn)一定的酸性或堿性,而上膠量又小,不能形成連接的一層時(shí),就可能發(fā)生這種情況。
2、小灰點(diǎn)。出現(xiàn)小灰點(diǎn)的可能性有兩種,一是輥筒不均勻造成膠的斑點(diǎn),二是油墨的不均勻造成的油墨沒有壓實(shí)的斑點(diǎn)。兩種可能性都和工藝有關(guān),可能通過調(diào)整工藝解決,提高上膠量的厚度。
3、小白點(diǎn)。一般表面的油墨的變色的情況下容易出現(xiàn)。多出現(xiàn)的鍍鋁膜的復(fù)合中。出現(xiàn)原因有二:一是油墨本身的遮蓋力不強(qiáng)或遮蓋不均勻,尤其是白油墨,使鋁的顏色滲透出來,沒有鋁的顏色滲透的地方形成小白點(diǎn);二是工藝原因,烘道溫度(特別是一級(jí)烘道)太高或上膠量太厚,導(dǎo)致在一級(jí)烘道內(nèi)膠層表面凝結(jié),乙酯在二、三級(jí)烘道中沖出來的時(shí)候,擠出膠水,顯出油墨本色。解決方法是提高油墨遮蓋力或者一、二、三級(jí)烘道調(diào)整適合的溫度,逐步升溫。避免一級(jí)溫度過高。
4、小晶點(diǎn)。小晶點(diǎn)發(fā)生在透明膜上的比較多,有凹凸兩種,成因不同:凸出來的小晶點(diǎn)大多是配膠原因,也可能是因?yàn)闄C(jī)器沒有清洗干凈。消除小晶點(diǎn)的方法是必須嚴(yán)格按照正確的配膠方法進(jìn)行配膠,機(jī)器使用后一定要清洗干凈;凹進(jìn)去的小晶點(diǎn),用放大鏡仔細(xì)觀察,就會(huì)發(fā)現(xiàn)其中有小氣泡,這主要是因?yàn)樗葸^多引起的。
5、小疤點(diǎn)。主要是由于膜活化處理不均勻的膜,在印刷過程中也出現(xiàn)同樣的疤點(diǎn),當(dāng)然也可能是因?yàn)榛罨瘯r(shí)間過長引起的。
6、波浪紋。波浪紋容易發(fā)生在白膜上,主要是因?yàn)槟z分子量不整齊,經(jīng)過熱烘道,熱輥筒后,有彈性的高分子鏈內(nèi)收縮,不同分子量的分子內(nèi)收縮不一致,這種內(nèi)收縮的不均勻引起波浪紋。出現(xiàn)這種情況應(yīng)考慮膠的原因。
7、薄膜對(duì)表面質(zhì)量的影響。由于薄膜的表面光滑程度,均勻程度的種種原因,可能會(huì)造成上述六種現(xiàn)象的類似現(xiàn)象。要區(qū)別是薄膜的原因還是上述六種情況,可以對(duì)沒有復(fù)膜的薄膜用放大鏡仔細(xì)觀察,由于透明的膠水在兩層膜之間,與兩層膜共同形成復(fù)合膜,用放大鏡,將原本很小的薄膜上的斑點(diǎn),波浪等放大,許多情形要仔細(xì)觀察才能發(fā)現(xiàn)問題。
三、復(fù)合膜的隧道現(xiàn)象
復(fù)合后由于薄膜的收縮,邊緣部分或中央部分象蚯蚓狀的脫層,稱之為復(fù)合膜隧道現(xiàn)象。出現(xiàn)這種現(xiàn)象的原因主要有以下幾個(gè)方面:
1、在復(fù)合過程中張力控制不良引起復(fù)合基材的復(fù)合后收縮且收縮比例相差較大時(shí),破壞了復(fù)合膜膠水層的粘接,產(chǎn)生隧道現(xiàn)象。解決辦法是在復(fù)合時(shí)應(yīng)根據(jù)不同復(fù)合基材的拉伸特性設(shè)定合適的張力。
2、薄膜起皺,厚薄不均,在復(fù)合時(shí)為了不使復(fù)合膜起皺,加大張力進(jìn)行復(fù)合從而導(dǎo)致復(fù)合膜隧道。解決辦法是在復(fù)合時(shí)檢查薄膜的放卷時(shí)的狀態(tài),如出現(xiàn)薄膜起皺、抖邊等現(xiàn)象的不使用。
3、粘合劑的分子量小,導(dǎo)致復(fù)合膜的初粘力低,從而引起復(fù)合膜的隧道現(xiàn)象。解決辦法是選用高分子量、高凝聚力、快速固化的粘合劑。
4、由于粘合劑涂布量過多,復(fù)合膜經(jīng)熱合輥后未完全冷卻,粘合劑層還有一定的流動(dòng)性,從而引起復(fù)合膜的隧道現(xiàn)象。解決辦法是適當(dāng)降低粘合劑的涂布量。
四、復(fù)合膜的爽滑性差。
復(fù)合膜的爽滑性差,膜之的磨擦力大,降低了復(fù)合膜的開口性能、操作性能。出現(xiàn)復(fù)合膜爽滑性差的原因主要有:
1、復(fù)合膜的熟化溫度太高。處理方法:降低熟化溫度,熟化溫度最好不要超過50℃,如時(shí)間允許,可自然熟化的更好。
2、復(fù)合基材爽滑性差。處理方法:復(fù)合膜噴粉。
3、復(fù)合膜吸潮。處理方法:注意儲(chǔ)存、運(yùn)輸過程中不要粘到水,室內(nèi)濕度過大時(shí)要注意復(fù)合膜防護(hù)。
五、復(fù)合膜起皺。引起復(fù)合膜起皺的原因。
1、復(fù)合基材本身起皺。處理方法:復(fù)合時(shí)注意檢查復(fù)合膜的狀態(tài),如有厚薄不均、荷葉邊、起皺等現(xiàn)象時(shí)不使用。
2、導(dǎo)輥、復(fù)合輥不平衡引起復(fù)合膜起皺。處理方法:檢查調(diào)整各導(dǎo)輥、復(fù)合輥使其平衡。
擠出復(fù)合常見問題及處理方法
一、復(fù)合強(qiáng)度差
復(fù)合強(qiáng)度差的原因:
1、樹脂表面氧化不足。對(duì)策:提高樹脂溫度;降低生產(chǎn)線速度;增大氣隙(氣隙指的是從T型鏡頭的??诘綇?fù)合輥與冷卻輥的切線之間的距離)。
2、樹脂溫度過低。對(duì)策:提高樹脂溫度;提高背壓(樹脂壓力);檢查加熱器有無故障。
3、復(fù)合壓力不足。對(duì)策:提高復(fù)合壓力。
4、AC劑干燥不完全。對(duì)策:提高干燥溫度;降低線速度;增大干燥風(fēng)良。
5、基材的表面活性不夠,電暈值低。對(duì)策:上機(jī)生產(chǎn)前用電暈筆或電暈測(cè)試液檢測(cè)基材的電暈處理值,達(dá)不到要求的基材不使用。
二、復(fù)合厚薄不均
原因主要有:
1、T型模口溫度設(shè)定不當(dāng)。對(duì)策:調(diào)整T型??谠O(shè)定溫度。
2、T型??诘哪O恫痪鶆颉?duì)策:調(diào)整T型??诘哪O?。
3、T型模頭模口粘臟。對(duì)策:停機(jī)清理???。
三、復(fù)合起皺
復(fù)合起皺的原因:
1、復(fù)合硅膠輥損傷或圓度不好。對(duì)策:打磨或更換復(fù)合硅膠輥。
2、導(dǎo)輥不平衡。對(duì)策:檢查、調(diào)整各導(dǎo)輥,使導(dǎo)輥平衡。
3、線速度過低。對(duì)策:提高線速度。
4、張力太小。對(duì)策:增大張力。
5、原材料的問題。對(duì)策:更換原材料。
四、復(fù)合膜透明度差
復(fù)合膜透明度差的原因:
1、擠出機(jī)擠出溫度太低,造成樹脂塑化不良。對(duì)策:根據(jù)樹脂性能特點(diǎn)及實(shí)際生產(chǎn)情況來設(shè)置和控制相應(yīng)的擠出溫度,保證樹脂塑化良好,這是提高復(fù)合膜透明度的前提條件之一。
2、冷卻鋼輥表面溫度太高,冷卻效果太差,使復(fù)合膜透明度大打折扣。對(duì)策:適當(dāng)降低冷卻水的溫度及冷卻鋼輥的表面溫度。一般來說,冷卻水的溫度控制在20℃以下,冷卻剛輥的表面溫度控制在60℃以下。
3、基材本身的透明度不好。對(duì)策:更換透明性好的基材。
五、復(fù)合膜凝膠及魚眼斑。
原因:
1、擠出機(jī)溫度設(shè)置不當(dāng),特別是模頭和樹脂的溫度太低,造成樹脂塑化不良,使熔融樹脂出現(xiàn)鯊魚皮現(xiàn)象或者類似魚眼狀的斑痕。對(duì)策:將擠出機(jī)的擠出溫度和樹脂的溫度調(diào)整到適當(dāng)值,保證樹脂塑化良好。
2、樹脂中含有水分,影響樹脂的塑化狀況。對(duì)策:對(duì)樹脂進(jìn)行攪拌或烘干,去除其中所含的水分,使樹脂能夠充分塑化。
3、樹脂中溫進(jìn)熔融指數(shù)或密度不同的其他樹脂,使樹脂塑化不好或塑化不完全。對(duì)策:更換熔融指數(shù)和密度適當(dāng)?shù)臉渲?/p>
4、更換樹脂對(duì)沒有將料筒徹底清洗干凈,料筒中殘存的其他樹脂或雜質(zhì)對(duì)樹脂塑化狀況產(chǎn)生不良影響。對(duì)策:徹底清洗料筒,去除雜質(zhì)等影響。
高工作濃度涂布在復(fù)合工藝中的應(yīng)用
一、膠粘劑的選擇
以往,國內(nèi)使用的干式復(fù)合膠粘劑多為聚氨酯系列雙組分膠粘劑,其分子量和粘度都比較高,固含量一般在50%-65%之間。而目前市場(chǎng)上應(yīng)用最廣的是高固含量低粘度膠粘劑,其分子量和粘度較低,固含量一般在70%-75%之間。
依據(jù)實(shí)際生產(chǎn)情況,高工作濃度涂布用膠粘劑的選擇可以從以下幾個(gè)方面考慮。
1、粘度
在高工作濃度涂布時(shí),如果膠液的粘度較高,可能會(huì)造成涂布不均勻,影響復(fù)合產(chǎn)品性能;粘度太低,可能會(huì)因分子量小造成其他性能不穩(wěn)定。所以,在實(shí)際生產(chǎn)中,生產(chǎn)企業(yè)要依據(jù)自身生產(chǎn)條件和工藝要求,經(jīng)多次小批量測(cè)試并能滿足預(yù)計(jì)要求后才能大批量生產(chǎn),以防造成巨額損失。
2、初粘力
在復(fù)合生產(chǎn)中,復(fù)合膜剛下機(jī)時(shí)一般要求有一定的剝離強(qiáng)度,否則復(fù)合膜可能會(huì)出現(xiàn)隧道現(xiàn)象,造成次品。高工作濃度涂布中,針對(duì)不同類型的復(fù)合基材,要求選擇的膠粘劑也要具備相應(yīng)的初粘力,一般情況下要求在1.0N/15mm以上為宜。
3、固化時(shí)間
由于兩種或多種復(fù)合基材的結(jié)構(gòu)不同,實(shí)際生產(chǎn)中的固化時(shí)間也不盡相同,固化時(shí)間的確定要依據(jù)生產(chǎn)企業(yè)的實(shí)際情況而定,如固化室的溫度、基材的類型、膠粘劑的綜合性能等。
二、涂布輥的選擇
在干式復(fù)合中,膠粘劑的干基涂布量是決定復(fù)合強(qiáng)度和復(fù)合膜性能的關(guān)鍵,所以,生產(chǎn)某種結(jié)構(gòu)或用途的復(fù)合包裝,膠粘劑的涂布量必須要達(dá)到一定的數(shù)值(可以稱為基本涂布量),否則可能無法滿足使用要求。
上膠量的經(jīng)驗(yàn)公式如下:
式中,W為干基涂布量,μ為涂布輥的網(wǎng)穴深度,N為所用配制好的膠液濃度,D為膠液的密度。
涂布輥是膠粘劑基本涂布量的決定因素,如果膠粘劑的工作濃度較低,為了達(dá)到基本涂布量,只能通過選擇低網(wǎng)線數(shù),深網(wǎng)穴的涂布輥,以提高膠粘劑的濕膠量來保證復(fù)合強(qiáng)度和性能。而高工作濃度涂布恰恰相反,可以選擇高網(wǎng)線數(shù),淺網(wǎng)穴的涂布輥進(jìn)行涂布。
舉例來說,如果確定某產(chǎn)品的基本涂布量W為4.0g/m2,設(shè)定膠液的濃度N為38%,膠液密度D取1,則涂布輥的網(wǎng)穴深度為:
μ=5W/N·D=5×4.0/0.38×1.0=52.6μm
同時(shí),依據(jù)涂布輥的網(wǎng)穴深度,我們還可推測(cè)出涂布輥的網(wǎng)線數(shù)為150線/英寸。
值得注意的是,由于高工作濃度涂布一般要求用淺網(wǎng)穴的涂布輥。所以經(jīng)常會(huì)出現(xiàn)涂布輥網(wǎng)穴堵塞的問題,影響復(fù)合質(zhì)量。所以在生產(chǎn)過程中除了定期清洗涂布輥外。還有加強(qiáng)日常數(shù)據(jù)測(cè)試,驗(yàn)證涂布量,以便形成穩(wěn)定的生產(chǎn)工藝。
三、高工作濃度涂布的優(yōu)勢(shì)
1、減少乙酸乙酯用量,降低生產(chǎn)成本
例如一種普遍型雙組分聚氨酯膠粘劑,其主劑和固化劑的固含量為75%,配比為主劑:固化劑=4:1,重量為20千克,膠粘劑的單價(jià)為19元/千克,乙酸乙酯的單價(jià)為8元/千克,要求復(fù)合膜的干基涂布量為3.0g/m3。下面就來核算一下低工作濃度涂布和高工作濃度涂布時(shí)乙酸乙酯的用量及經(jīng)濟(jì)效益比較。
(1)設(shè)定低工作濃度涂布時(shí)膠液的工作濃度為28%,則乙酸乙酯的用量為:
(20×0.75)÷0.28-20=33.6千克,共計(jì)33.6×8=268.8元
(2)假設(shè)高工作濃度涂布時(shí)膠液的工作濃度為40%,則乙酸乙酯的用量為:
(20×0.75)÷0.40-20=17.5千克,共計(jì)17.5×8=140元
(3)對(duì)此上述兩種涂布工藝可知,高工作濃度涂布時(shí)每組膠粘劑可節(jié)省乙酸乙酯成本128.8元,按每班8小時(shí)生產(chǎn)可用5組膠粘劑計(jì)算,則每班可節(jié)省乙酸乙酯成本644元,經(jīng)濟(jì)效益非??捎^。
2、消除安全和衛(wèi)生隱患,提高生產(chǎn)效率
乙酸乙酯是易燃易揮發(fā)的有機(jī)溶劑,對(duì)人體健康也有很大危害,因此,減少乙酸乙酯的用量,能夠減少安全隱患和對(duì)人體的危害。另外,如果乙酸乙酯的用量過多,有可能造成復(fù)合膜中的溶劑殘留量過高,影響包裝內(nèi)容物的衛(wèi)生性。
如果乙酸乙酯的用量大,為保證其揮發(fā)徹底,則需要的干燥溫度要高,干燥風(fēng)量要大,同時(shí)要減慢復(fù)合速度,這勢(shì)必會(huì)影響生產(chǎn)效率。而高工作濃度涂布工藝由于減少了乙酸乙酯的用量,復(fù)合生產(chǎn)效率相應(yīng)也會(huì)提高。
3、提高復(fù)合膜的質(zhì)量
高工作濃度涂布時(shí),涂布在基材上的膠液量減少,涂膠層的厚度減少,避免或減少了膠粘劑在干燥過程中表面結(jié)皮的現(xiàn)象,可以提高復(fù)合膜的透明度。